L'origine du verre :
matière, composition, process de fabrication
La matière
Le verre est fabriqué à partir de matières premières naturelles inorganiques c’est-à-dire minérales. La très grande majorité des emballages en verre présents sur le marché est constituée de verre dit « commercial » ou « sodocalcique » (ex : bouteilles, bocaux).
Le verre est obtenu par fusion de :
- Sable
- Soude sous la forme d’oxydes alcalins
- Chaux
- Et de composants divers qui jouent sur la coloration du verre
La couleur du verre
Elle provient de deux origines : la composition des matières premières mises dans le four et l’introduction d’un « colorant » au moment de la coulée du verre.
Est-il possible de produire du verre recyclé blanc ?
Oui ! Le recyclage du verre en France permet de produire 3 couleurs principales de calcin : transparent, vert et ambré.
Pendant de longues années, les secteurs du luxe, de la cosmétique ou du vin rosé privilégiaient le verre extra-blanc, ne pouvant pas être produit à partir de calcin recyclé.
Mais les attentes des consommateurs sur les engagements environnementaux des marques sont de plus en plus fortes et les technologies des verriers progressent en ce sens.
Ainsi, plusieurs fabricants développent aujourd’hui de nouvelles gammes de bouteilles et flacons, à partir de verre recyclé (jusqu’à 25% de calcin post-consommation) à la luminance proche d’un verre extra-blanc classique.
À noter également l’existence de verre blanc contenant jusqu’à 40% de calcin post-consommation.
La fabrication du verre recyclé : les étapes
Le traitement du verre se passe en 2 étapes : la préparation du calcin puis son incorporation dans les fours verriers.
ÉTAPE 1 : LA PRÉPARATION DU CALCIN
À son arrivée dans le centre de traitement, le verre subit toute une série de tri :
- Un premier tri avec des machines spécifiques, pour écarter les métaux ferreux et non-ferreux (acier, aluminium...).
- Ces métaux sont ensuite envoyés aux recycleurs dédiés.
- Un second tri optique au laser identifie et extrait les matériaux infusibles : porcelaine, grès, céramique, etc.
- Un soufflage permet ensuite d’éliminer les éléments légers : les bouchons, le papier des étiquettes, etc.
- Un tri complémentaire, appelé le démélange, permet de séparer le verre de couleur du verre incolore, pour la fabrication de nouveaux emballages de teinte claire.
- Le verre est enfin transformé en calcin, calibré à la demande des verriers pour refaire des emballages en verre.
ÉTAPE 2 : LES FOURS VERRIERS
1/ Les emballages en verre sont ensuite fabriqués dans des fours à bassin pouvant atteindre une capacité de production de 450 à 480 tonnes par jour.
2/ Les matières nécessaires à la fabrication sont introduites dans le four, avec une température de fusion comprise entre 1 300 °C et 1 550 °C.
3/ Après la fusion vient le moulage, permettant de fabriquer les emballages.
4/ Enfin, la recuisson refroidit le verre dans des conditions optimales pour éviter les risques de fissures et obtenir un emballage résistant.
5/ Un contrôle qualité rigoureux est réalisé à chaque étape de la fabrication, afin de garantir la conformité du verre et de répondre aux exigences croissantes des clients.
Focus sur la fabrication du verre d’emballage
Source : Verre Avenir
Le saviez-vous ?
En fonction des régions, le gisement et la qualité du verre ne sont pas les mêmes : par exemple, dans la région Hauts-de-France, le gisement de verre est plutôt coloré (apporté par les bouteilles de bière) alors que dans le Sud de la France, le gisement est d’avantage blanc (bouteilles de rosé).
Ainsi, chaque centre de traitement a un procédé et un savoir-faire qui lui est propre et adapté au verre d’emballage collecté.
En découvrir plus sur le verre
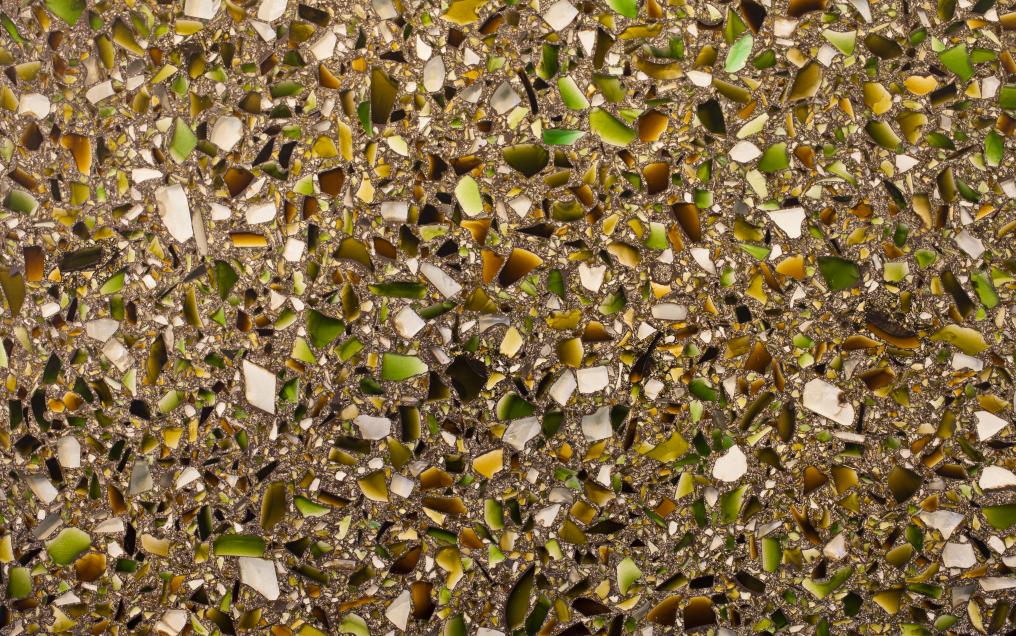
État des lieux, tri, collecte, boucle du recyclage
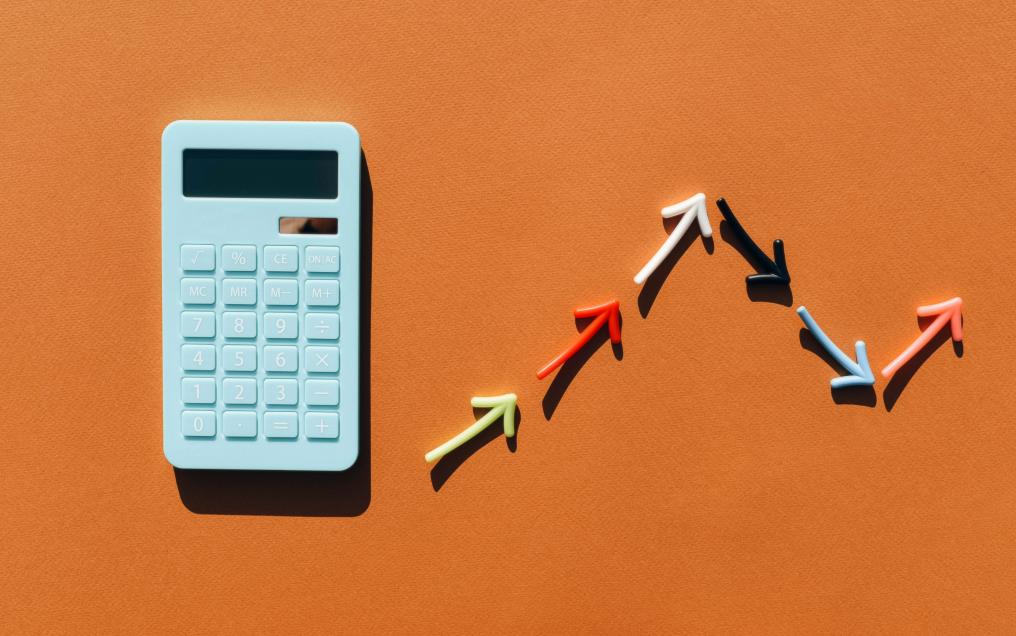
Taux de recyclage, bénéfices environnementaux, actions de réduction (infographie)
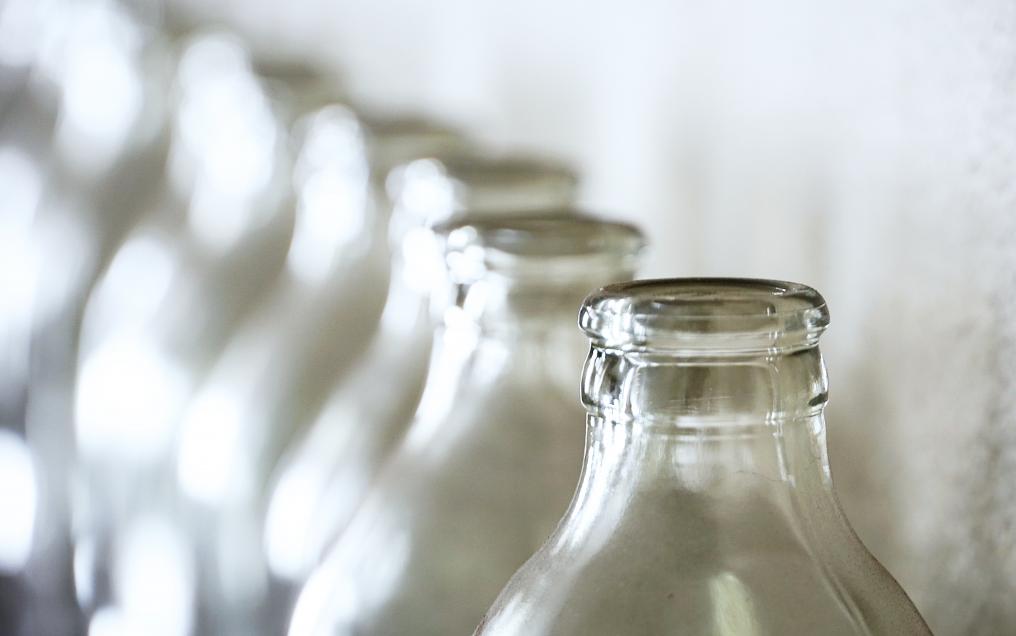
État des lieux et perspectives, réglementation, initiatives du secteur
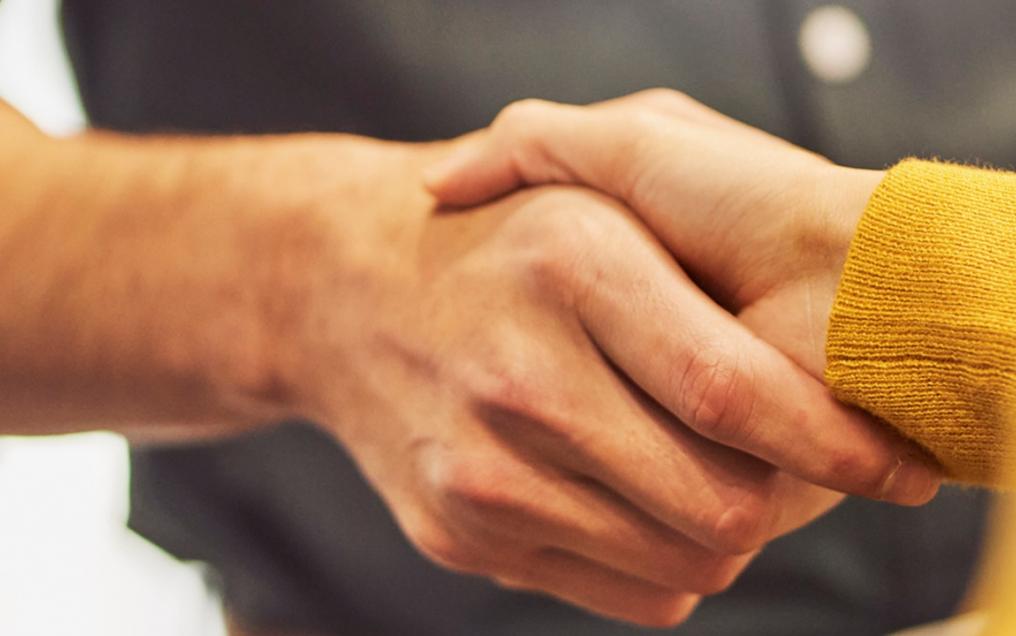
24 acteurs de la filière verre signent une charte d'engagement : 100% de recyclage à horizon 2029